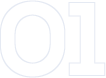
Adoption of Solar Photovoltaic Energy Systems
By integrating advanced solar photovoltaic panels across our facility’s rooftops, we generate approximately 1,214,038 kWh of clean, renewable energy annually. This initiative reduces our carbon footprint by an estimated 365.5 tonnes of CO2 emissions each year, with 20% of our facility’s energy needs powered by solar energy.
Challenge: Enhance energy efficiency and minimize energy consumption.
Solution: Deploy state-of-the-art rooftop solar photovoltaic systems to produce sustainable, renewable energy.
Impact: Achieved annual energy savings of 1.2 million kWh, cutting CO2 emissions by 365.5 tonnes. Approximately 20% of the facility’s energy is sourced from solar power, reinforcing our commitment to environmental stewardship.